Preventative maintenance has become a watchword in the maritime industry. It offers the ability to make minor adjustments to a piece of equipment as time goes on. In an ideal world, machinery would not move, except to do useful work; but unfortunately, sometimes it does. The angle of a driveshaft might change slightly, or gears might engage in a slightly different way. With preventative maintenance, operators can make minor alterations to account for this, and generally the solutions are considered to be rather high-tech; sensor readings, algorithms, big data, remote monitoring.
But especially on a moving platform like a ship, with heeling and bobbing motions leading to unpredictable patterns of wear and assets a long way from shore, this industry has had to develop ways to deal with these problems on the fly. Sensors and remote diagnostics are relatively recent; but a lower-tech solution can sometimes work just as well.
One of these is variable chocking. It is far from innocuous. Most engines in an industrial setting are rafted on a series of chocks, which absorb vibration, maintain correct driveshaft and gear positioning, and eliminate shock from both within and without a marine asset such as an engine. Sometimes, chocks are cast from epoxy, forming a static structure which must be replaced should things get out of alignment. But on occasion, a complex application will demand a more elegant solution.
Handling the pressure
Recently, SKF was contacted to provide a chocking solution for one of the most demanding types of vessels, in terms of maintenance: a seabed mining vessel, or to be more exact, a diamond miner.
There are a large number of things which must go right to run these types of vessels, because unlike other ship types there are two major contact points with the sea, rather than just propulsion. Seabed mining ships have to stay in place even in tumultuous seas, experiencing near-constant and variable torques and shearing forces from the mining equipment as well as from the propulsion, which acts to anchor the vessel in place.
The customer chose SKF Vibracon stainless-steel chocks to handle this application, using them to mount the main drive electric motor which handles the propulsion. Each motor is supported by four Vibracon chocks mounted in combination with the SKF spherical washers to avoid bending forces in the foundation bolts.
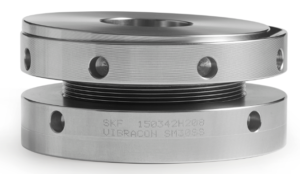
SKF Vibracon re-adjustable chock
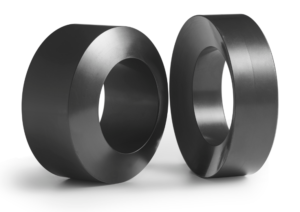
SKF Spherical Washer (set)
Vibracon chocks are standardised, making them fast to deliver; but offer variable geometry to allow them to account for the inevitable marginal discrepancies that occur between the ship’s design documents and the real-life layout. Because the variable chocks were chosen, their installation was much faster than an epoxy casting would have been.
“The Vibracon chocks are used in this application to make the chocking procedure easier and faster,” explains Zachry Viljoen, Sales Engineer – SKF South Africa.
This unusual use case still allowed SKF to leverage the benefits of a faster installation, and allows different positions to be tested in order to ensure alignment is precisely correct, down to fractions of a millimeter – as opposed to relying on an epoxy casting to be right first time.
„A stitch in time…“
In the majority of cases though, Vibracon allows machinery to be adjusted as time goes along, on the fly, without making a return to the shipyard. This preventative maintenance approach has become a popular one, as though it requires a litttle more forward-thinking and a degree of speculation, it could prevent a potentially major – even catastrophic in some cases – downtime incident. On the other hand, a straightforward epoxy casting would not allow such alterations to be made without a visit to a shipyard.
For applications where machinery is too large to be altered in the field, epoxy casting still has a place,“ Viljoen explains. „However on smaller motors and pumps adjustments can be made using Vibracon cocks, if alignment tools are available.“
„Traditional non-epoxy applications would also show a savings benefit by reusing the chocks,“ he adds.
Returning to a shipyard every so often for a tailor-made, from-scratch solution can be very costly. For shipowners, it may well be worth considering how variable geometry componentry on board, combined with a little foresight, and a sensible approach to predictive maintenance can spare them costs and downtime in the long run.